Synchronous Motors: Understanding the Basics
Synchronous motors are a type of electric motor that operates at a constant speed, regardless of the load. These motors are designed to work in synchronization with the power supply frequency, hence the name. They are widely used in various industries due to their high efficiency, reliability, and torque-to-weight ratio. In this article, we will delve into the basics of synchronous motors, their key components, and how they work.
Key Components of Synchronous Motors
The main components of a synchronous motor include the rotor, stator, and inverter. The rotor is the moving part of the motor, while the stator is the stationary part. The inverter is an electronic device that converts the AC power supply into DC power for the motor. The rotor and stator are designed to work in synchronization, which is achieved through the use of magnetic fields.
How Synchronous Motors Work
Synchronous motors work on the principle of electromagnetic induction. When an alternating current (AC) flows through the stator, it creates a rotating magnetic field. This magnetic field interacts with the rotor, causing it to rotate. The speed of the rotor is determined by the frequency of the AC power supply. To maintain synchronization, the rotor must rotate at the same speed as the magnetic field.
Benefits of Synchronous Motors
Synchronous motors offer several benefits over other types of electric motors. They have a high torque-to-weight ratio, which means they can produce more torque relative to their size and weight. This makes them ideal for applications where space is limited but high torque is required. Additionally, synchronous motors are highly efficient, resulting in lower energy consumption and reduced operating costs. They are also reliable and require minimal maintenance, making them a cost-effective option in the long run.
Conclusion
Synchronous motors are a versatile and efficient option for various industrial applications. Their high torque-to-weight ratio, high efficiency, and reliability make them an attractive choice for industries requiring precise control and high performance. By understanding the basics of synchronous motors, including their key components and how they work, businesses can make informed decisions when selecting the right motor for their needs.
The Science Behind Synchronous Motor Design
Synchronous motors are a type of electric motor that operates at a constant speed, regardless of the load. This is achieved through the synchronization of the rotor’s rotational speed with the rotating magnetic field. The key components of a synchronous motor include the rotor, stator, and inverter. The rotor is the moving part of the motor, while the stator is the stationary part. The inverter is an electronic device that converts DC power to AC power, which is necessary for the motor’s operation. The interaction between the rotor and stator magnetic fields creates torque, causing the rotor to rotate. The inverter ensures that the stator’s magnetic field is constantly adjusted to maintain synchronization with the rotor’s speed. This synchronization is crucial for the motor’s efficiency and reliability. The science behind synchronous motor design involves understanding the principles of magnetic fields, electromagnetic induction, and the importance of maintaining synchronization between the rotor and stator. This understanding allows engineers to design and manufacture synchronous motors that are highly efficient, reliable, and suitable for a wide range of applications. By leveraging the principles of synchronous motor design, manufacturers can create motors that provide high torque-to-weight ratios, high efficiency, and low maintenance requirements, making them an attractive option for industries such as renewable energy, automotive, and industrial automation.

Low-Speed High-Torque Applications: Where Synchronous Motors Excel
Synchronous motors have proven to be highly efficient in low-speed high-torque applications, making them a preferred choice for industries that require precise control and high reliability. These motors are designed to operate at a constant speed, regardless of the load, which makes them ideal for applications where speed variation is not necessary or desirable. In this context, we will explore how synchronous motors excel in these specific applications and why they are increasingly being adopted across various industries.
One of the primary advantages of synchronous motors in low-speed high-torque applications is their ability to provide high torque at low speeds. This characteristic allows them to efficiently handle heavy loads without overheating or experiencing significant wear and tear. As a result, synchronous motors are often used in conveyor systems, cranes, and elevators, where high torque is required to lift or move heavy objects at slow speeds.
Another significant benefit of synchronous motors in these applications is their high efficiency. Unlike traditional induction motors, which can experience a decrease in efficiency at lower speeds, synchronous motors maintain their efficiency across a wide range of speeds. This means that they consume less energy to produce the same amount of torque, resulting in cost savings and reduced environmental impact.
Reliability is also a critical factor in low-speed high-torque applications, as downtime can lead to significant operational disruptions and financial losses. Synchronous motors are designed with reliability in mind, featuring robust construction and fewer moving parts compared to traditional motors. This reduces the risk of mechanical failure and ensures continuous operation even under demanding conditions.
Furthermore, synchronous motors offer precise control over speed and torque, which is essential in applications where precise positioning and smooth operation are critical. For instance, in conveyor systems, synchronous motors can be programmed to maintain a consistent speed, ensuring that products are moved efficiently and safely. Similarly, in crane operations, precise control over torque and speed helps prevent accidents and ensures safe lifting practices.
Finally, synchronous motors are highly adaptable and can be easily integrated into various control systems. This flexibility makes them suitable for a wide range of low-speed high-torque applications, from industrial automation to renewable energy systems. In wind turbines, for example, synchronous motors can optimize energy production by adjusting speed and torque according to wind conditions, maximizing efficiency and reducing wear on the turbine blades.
In conclusion, synchronous motors have emerged as a preferred choice for low-speed high-torque applications due to their high torque-to-weight ratio, high efficiency, reliability, precise control, and adaptability. As technology continues to advance, it is likely that synchronous motors will become even more prevalent in industries requiring efficient and reliable operation. By understanding the principles and benefits of synchronous motors, engineers and industry professionals can make informed decisions when selecting the most appropriate motor technology for their specific needs.
Permanent Magnet Synchronous Motors: A High-Efficiency Solution
In the realm of synchronous motor technology, permanent magnet synchronous motors (PMSMs) stand out as a high-efficiency solution. These motors are designed with a permanent magnet as the rotor and a three-phase current-carrying stator. The interaction between the magnetic fields of the rotor and stator results in torque production, making them highly efficient and reliable. PMSMs are widely used in various industries due to their numerous advantages.
One of the primary benefits of PMSMs is their high power density. This means they can deliver a significant amount of power relative to their size and weight, making them ideal for applications where space is limited. Additionally, PMSMs boast high efficiency, which translates to lower energy consumption and reduced heat generation. This not only saves energy but also increases the motor’s lifespan by minimizing thermal stress.
Another advantage of PMSMs is their low maintenance requirements. Since they do not have brushes or commutators, they are less prone to wear and tear compared to other types of motors. This reduces the need for frequent repairs and replacements, resulting in lower operational costs and increased uptime. Furthermore, PMSMs are known for their high reliability, ensuring consistent performance over an extended period.
The use of PMSMs can be seen in various industries. For instance, in the renewable energy sector, PMSMs are often used in wind turbines due to their high efficiency and reliability. In the automotive industry, PMSMs are employed in electric vehicles, providing the necessary torque and efficiency for optimal performance. Industrial automation also benefits from the use of PMSMs, as they offer precise control and high efficiency in applications such as conveyor systems and robotics.
However, despite their numerous advantages, PMSMs also have some limitations. One of the main challenges is the high cost of rare-earth magnets used in their construction. This can make them less accessible to some users. Moreover, PMSMs require sophisticated control systems to maintain synchronization, which can add complexity and cost to the overall system.
Nevertheless, the benefits of PMSMs far outweigh their drawbacks. Their high power density, high efficiency, and low maintenance requirements make them an attractive option for various applications. As technology continues to advance, it is likely that the cost of rare-earth magnets will decrease, making PMSMs even more viable. In conclusion, PMSMs are a high-efficiency solution in the realm of synchronous motor technology, offering numerous advantages that make them a preferred choice in various industries.
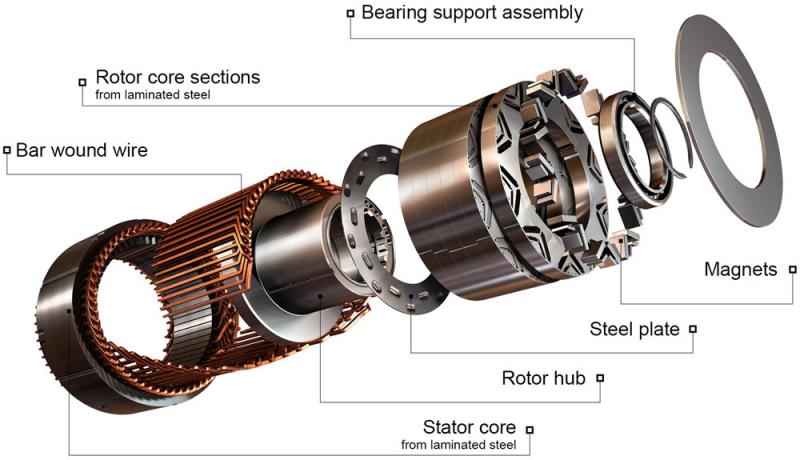
Reliability and Maintenance: Synchronous Motor Considerations
Synchronous motors are known for their high reliability and efficiency, making them a preferred choice in various industries. However, like any other machine, they require proper maintenance to ensure optimal performance and extend their lifespan. Regular inspections and maintenance can significantly reduce downtime and costs associated with repairs or replacements.
One of the key considerations for synchronous motor maintenance is the condition of the bearings. These components are critical as they support the motor’s shaft and facilitate smooth rotation. Over time, bearings can wear out due to friction and heat, leading to increased vibration and noise. Regular inspection and replacement of worn-out bearings can prevent damage to other motor components and maintain efficiency.
Another critical aspect of synchronous motor maintenance is the electrical system. The stator windings and rotor magnets are prone to damage from overheating, moisture, and electrical surges. Monitoring the motor’s temperature and ensuring that it operates within the recommended temperature range can help prevent overheating. Additionally, protecting the motor from moisture and ensuring that the electrical connections are secure can prevent electrical faults.
Inverter maintenance is also crucial for synchronous motor operation. The inverter is responsible for controlling the motor’s speed and torque. Failure of the inverter can result in motor failure or inefficient operation. Regular checks on the inverter’s components, such as power electronics and control circuits, can help identify potential issues before they cause problems.
Proper installation is also vital for synchronous motor reliability. Incorrect installation can lead to misalignment, vibration, and premature wear of components. Ensuring that the motor is installed according to the manufacturer’s specifications can help prevent these issues and ensure optimal performance.
Finally, selecting high-quality synchronous motors and components is essential for reliability and maintenance. Choosing motors from reputable manufacturers and using high-quality components can significantly reduce the risk of failure and extend the motor’s lifespan.
In conclusion, synchronous motors offer numerous benefits, including high efficiency, reliability, and high torque-to-weight ratio. However, they require proper maintenance to ensure optimal performance and extend their lifespan. Regular inspections, proper installation, and selecting high-quality components are critical for maintaining synchronous motor reliability and efficiency.
Huawei and Siemens: Real-World Examples of Synchronous Motor Applications
In the realm of synchronous motor technology, companies like Huawei and Siemens have made significant strides in utilizing these high-efficiency motors in various industries. These companies’ products showcase the benefits of synchronous motors, including high efficiency, reliability, and torque-to-weight ratio.
For instance, Huawei’s innovative synchronous motor technology is used in their wind turbines, which are designed to maximize energy output while minimizing environmental impact. By leveraging the high efficiency of synchronous motors, Huawei’s wind turbines can generate more power from wind, making them a key player in the renewable energy sector.
On the other hand, Siemens, a leading global engineering company, uses synchronous motors in their industrial automation solutions. Their synchronous motor drives are designed to provide precise control and high efficiency in various applications, such as conveyor systems, pumps, and compressors. These drives enable industries to optimize their operations, reduce energy consumption, and enhance productivity.
Moreover, both companies have developed synchronous motor solutions for the automotive industry. In electric vehicles, synchronous motors offer a high torque-to-weight ratio, which is crucial for achieving high performance and efficiency. This technology allows for faster acceleration, longer driving ranges, and reduced energy consumption, making electric vehicles more appealing to consumers.
In conclusion, the use of synchronous motors by companies like Huawei and Siemens demonstrates the versatility and efficiency of this technology. By integrating synchronous motors into their products, these companies have been able to enhance performance, reduce energy consumption, and contribute to a more sustainable future.
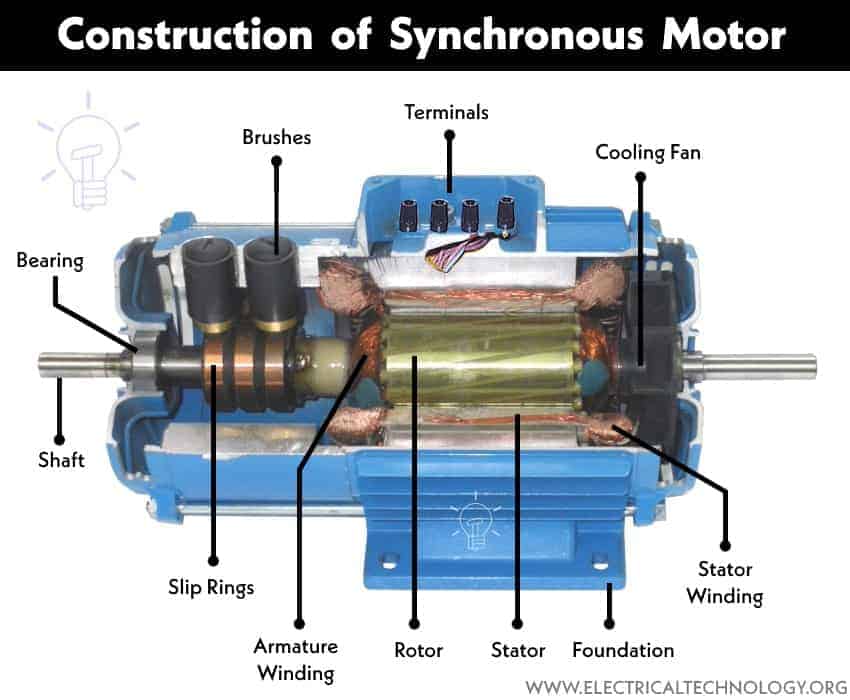
Designing and Implementing Synchronous Motor Control Systems
When designing and implementing synchronous motor control systems, several key considerations come into play. These include the choice of power electronics, control algorithms, and sensor systems. The selection of these components is crucial to achieving high-performance operation and optimizing motor performance.
In terms of power electronics, the choice of inverter technology is critical. The inverter converts DC power from the power source into AC power that is used to drive the motor. High-frequency switching devices such as IGBTs (Insulated Gate Bipolar Transistors) or power MOSFETs are commonly used in synchronous motor inverters due to their fast switching times and low power losses. These devices enable the creation of high-frequency AC waveforms that are necessary for efficient motor operation.
Control algorithms also play a vital role in synchronous motor control systems. These algorithms are used to control the motor’s speed, torque, and position. They can be implemented using various control strategies, such as vector control, direct torque control, or model predictive control. The choice of control algorithm depends on the specific application requirements and the desired performance characteristics of the motor.
Sensor systems are another essential component of synchronous motor control systems. These sensors provide feedback to the control system about the motor’s operating conditions, such as speed, position, and current. This information is used to adjust the motor’s operation to achieve optimal performance. Commonly used sensors include Hall effect sensors, optical encoders, and current sensors.
In addition to these components, the design of the motor itself is also critical. The motor’s design should be optimized for the specific application, taking into account factors such as the desired torque and speed range, the operating environment, and the required reliability and efficiency.
Overall, designing and implementing synchronous motor control systems requires careful consideration of several factors. By selecting the appropriate power electronics, control algorithms, and sensor systems, and optimizing the motor design for the specific application, it is possible to achieve high-performance operation and maximize the benefits of synchronous motor technology.
Realizing the Benefits of Synchronous Motor Technology
Realizing the benefits of synchronous motor technology is crucial for various industries, as it offers high efficiency, high reliability, and high torque-to-weight ratio. These motors have become increasingly popular due to their ability to provide optimal performance in different applications. To fully leverage the advantages of synchronous motor technology, it is essential to select the right motor and control system for your specific needs. This involves understanding the key components, such as the rotor, stator, and inverter, as well as the fundamental principles of synchronous motor design, including magnetic fields, electromagnetic induction, and synchronization between the rotor and stator. Additionally, considering the use of permanent magnet synchronous motors can further enhance efficiency and reduce maintenance requirements. Companies like Huawei and Siemens have successfully implemented synchronous motor technology in their products, demonstrating the potential for improved performance and efficiency in various industries. By employing best practices in designing and implementing synchronous motor control systems, including the choice of power electronics, control algorithms, and sensor systems, users can optimize motor performance and realize the full benefits of synchronous motor technology. Overall, synchronous motors offer a high-efficiency alternative to traditional AC and DC motors, making them an attractive option for companies seeking to enhance their operations and reduce energy consumption.